Equipment Training
Our team offers on-site training for newly installed equipment, helping your staff gain confidence and competence in using their tools from day one.
Why Training Matters
Proper training ensures your team can safely and efficiently operate newly installed equipment. We believe that the best results come from not just installing equipment, but empowering the people who use it every day.
Each session covers
Proper equipment operation
We guide your team through the correct operation of your newly installed equipment, step by step. This includes startup procedures, understanding control systems, and safe handling techniques. By the end of the session, your staff will know how to operate the equipment efficiently, reducing the risk of misuse or mechanical strain.
Safety procedures
Safety is at the core of every training session. We cover essential safety protocols for your equipment, including proper lifting practices, load limits, emergency shut off procedures, and hazard awareness. Our goal is to ensure every team member understands how to protect themselves and others while using the equipment.
Basic troubleshooting and maintenance
We teach your team how to identify and address common issues before they become major problems. Training includes daily checks, recognizing early warning signs, and basic maintenance tasks like lubrication, cleaning, and fluid level monitoring. This proactive approach minimizes downtime and extends equipment lifespan.
Best practices for daily use
To keep your operation running smoothly, we share practical, time tested tips for everyday use. From proper load balancing to consistent inspection routines, we help your team form habits that improve efficiency, prevent wear and tear, and promote a safer, more productive work environment.
Ongoing Support
We’re here even after the training ends. Our team offers continued guidance, follow-up visits, and service support as your operations evolve.

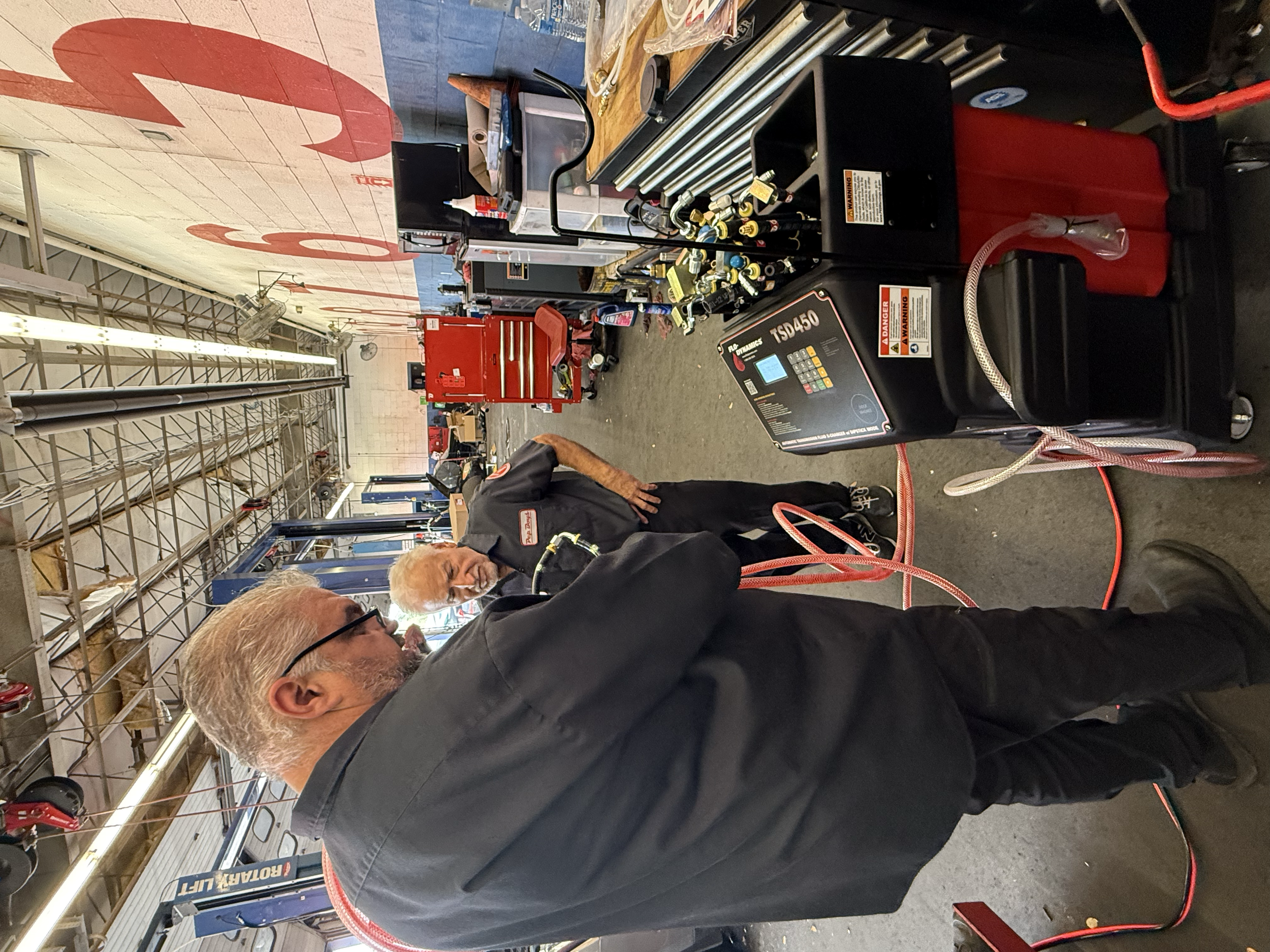

